ニュース
次世代自動車向けに高耐熱・高絶縁性樹脂の均一電着コーティング技術を開発【三菱マテリアル】
2019年3月25日
三菱マテリアル株式会社(取締役社長:小野 直樹、資本金:1,194億円)は、電気自動車コイルデバイスの高機能化および小型化に繋がる、金属導体へ高耐熱・高絶縁樹脂を均一にコーティングする電着技術を開発しましたので、お知らせいたします。
電気自動車・ハイブリッドカー用のパワーインダクター(※1)やリアクトル(※2)、モーターに用いられるコイルには、高温下での高い絶縁信頼性が要求され、近年、さらにそれらコイルデバイスの小型化に伴い、従来よりも複雑な形状の導体に絶縁加工を施すコーティング技術が求められていました。
複雑な形状の導体に絶縁被覆するため、これまでのポリイミド樹脂やポリアミドイミド樹脂の電着液は、電着しやすいように樹脂自体が加工されており、本来期待される高い耐熱性が得られず、高耐熱で高絶縁性を有する皮膜をコーティングできる電着技術はありませんでした。
このたび当社は、高い耐熱性を維持できるポリアミドイミド樹脂を用いた電着液を新たに開発するとともに、そのコーティングプロセスを最適化することで、例えば15以上の大きなアスペクト比(※3)を持つ平角線材や、屈曲形状の導体部材(モーターコイル、バスバー(※4))に、高耐熱・高絶縁性を有する(図1)樹脂皮膜を均一にコーティングする(図2)電着技術を開発しました。
当社は、本コーティング技術により、過酷な熱・電気的環境に耐えられる樹脂皮膜を従来よりも複雑な形状の導体にコーティングした部材を提供することが可能となり、今後加速する電気自動車・ハイブリッドカー用コイルデバイスの高機能化および小型化に大きく貢献できるものと考えております。
当社グループは、長期経営方針において、「ユニークな技術により、人と社会と地球のために新たなマテリアルを創造し、循環型社会に貢献するリーディングカンパニー」となることを目指しております。今後も独自の技術を活かした製品開発により、社会に貢献してまいります。
※1 パワーインダクター:電源回路でノイズ抑制や整流、平滑のために使用するデバイス。
※2 リアクトル:バッテリーとモーター・発電機間で、電圧を昇降圧するデバイス。
※3 アスペクト比:矩形(くけい)のものの長辺長さと短辺長さの比。
※4 バスバー:板状の配線用導体材料。
図1 コーティングした樹脂皮膜を200℃で保持した際の時間と絶縁破壊電圧の低下割合
(初期値100%)
図2 複雑な形状の導体へコーティングした樹脂皮膜の厚み
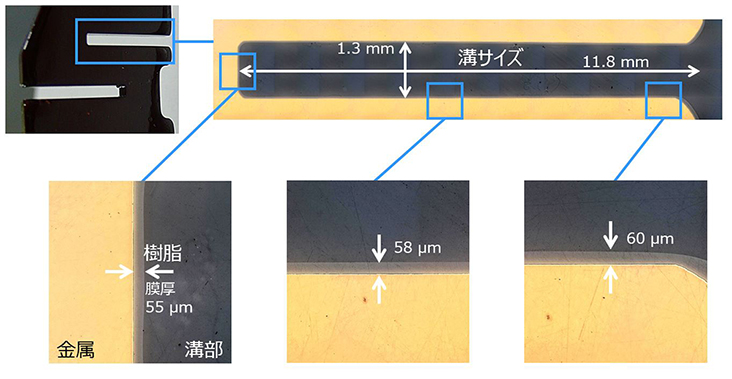
三菱マテリアル株式会社ホームページはこちら